Overview - SR3 to SR4
The SR3 testing at Jeff Jones Square in Sandpoint and at Marquette University in Milwaukee has been completed. We are grateful to the city of Sandpoint and all residents and visitors who served as our testers on this pilot project. This “real life test” gave us the information we needed to make important improvements to the design for SR4. We’ll share what we’ve learned, along with some insight into the array of civil engineering tests performed at Marquette.
The biggest challenge that we’ve found has been the manufacturing process. Each individual part worked fine, but putting everything together and subjecting them to the manufacturing process created some problems and a very challenging learning curve.
There are three fundamental features of the Solar Road Panels: the LED functionality, surface heating, and solar harvesting. Here’s what we’ve learned about each from the Sandpoint pilot project:
LED Functionality
SR3 has an array of LEDs, including red, green, blue, white, and yellow. Other colors and shades can be created by mixing the standard colors – we created a few extras for SR3 and will be working with more colors with SR4. These are individual high brightness LEDs designed for outdoor use. They worked great in all preliminary testing. We could turn them up so bright that they could actually hurt your eyes outside on a very sunny day. During SR3 testing, we worked to determine the optimal brightness levels for the LEDs in different situations. Now they automatically adjust themselves to the ambient light and we are pleased with how that is working.
The heavy vacuum of the lamination process is a very harsh environment for small electronics. The tiny LEDs were being damaged during this process. We experimented with many types of clear epoxies to protect them from the lamination process. We eventually found one that could handle the job and began producing panels.
When we initially installed the 30 panels at Jeff Jones Square, we programmed them to rotate through a series of patterns. It resembled a moving dance floor and the kids loved it. Later, we began to create some static images such as this earth design:
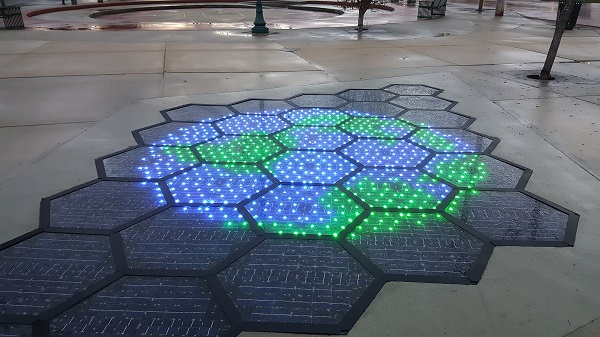
We left this up for 2-3 weeks, when we noticed something unusual: the blue LEDs began to fade (lower their intensity). Experimenting with other patterns, we noticed the same thing happening with the white and yellow LEDs. The red and green LEDs were not affected. This was confusing and frustrating, and we could not continue manufacturing panels until this was resolved.
After many conversations with the LED manufacturer, we learned that the blue, yellow, and white LEDs were made differently than the green and red LEDs. Together, after much testing, we came to the conclusion that the protective epoxy was having a chemical reaction with the LEDs and the sun was the catalyst.
This has been corrected for the SR4 design so that protective epoxies are no longer needed.
Heating
After two north Idaho winters, we’ve learned quite a lot with the heat testing results. Although SR3 was able to keep up with the snow in most situations, we’re increasing the heating capability of SR4 to allow for faster heating. This will allow the panels to more easily keep their temperatures up during heavy snowfall.
The Sandpoint installation used anodized aluminum panel retainers between the panels. Since there is no heating in the gaps between the panels, these metal pieces took on the ambient temperature. We learned that they could create an ice bridge during really heavy snowfall combined with extremely low temperatures. We’ve designed a rubber replacement – a “t-channel” for the aluminum units. This new design also greatly simplifies installation and maintenance.
Solar Harvesting
The most disappointing aspect of the pilot project in Sandpoint has been the energy harvesting. In order to increase the number of solar cells in the SR3 panel (SR2 was 36-watts and SR3 is 44-watts), we used a parallel/series combination of cell connections. We also created a Consolidator Board to consolidate the power collected by the panels. We used a parallel/series combination on this board to create the power input requirements for the micro-inverters.
Although all technical solar information I have found says that you can parallel solar power, we found that to be a very bad idea. All of the SR2 panels had their solar cells connected in series, so we’d never seen this problem. What we found was this: every panel produced power, but we couldn’t get them to combine properly to meet the input requirements of the micro-inverters. We were never able to “see” more than 1/3 of the power being produced. In addition, we learned that the extra laminate that was used in SR3 as compared to SR2 due to design changes interfered with solar gain. These problems have been eliminated with the new SR4 design.
For SR4, we found a way to maximize the solar cell area while maintaining a series-connected system. We also increased the wattage from 44W (SR3) to 50W (SR4). In addition, we’ve going from 17.6-percent efficient solar cells (SR3) to 22.5-percent efficient solar cells (SR4). We’ll always be able to increase the solar gain over time as the solar industry continues to advance and make more efficient products for us to incorporate. All of this means that we’ll be able to produce a lot more power with the SR4 panels.
We’ve also replaced the energy monitoring system with a more “Solar Road Panel friendly” monitoring system: one with a much larger input range that doesn’t require the parallel/series configurations.
When we get the SR4s installed, we’ll activate the system on the city’s website. For now, the current energy monitoring system reads zero because the panels have been disconnected from it.
Additional SR4 Improvements
Another hard lesson learned: the cables that were used with the SR3 panels had a plastic jacket. Over time, this plastic jacket became brittle and cracked, allowing water into the cable. After several months, some of the panels began to fail. We’d see only half of the panel lit up. Eventually, the LED patterns would become corrupted and the panel could no longer be communicated with.
We began removing the damaged panels and inspecting them. We found damaged cables where water had entered and began corroding the wires inside. This corrosion creates resistance, which in turn robs the panels of power. This means that the microprocessor, the LEDs, and the heating elements are not receiving the power that they need to function properly.
The new SR4 design uses and molded rubber cable which remains much more flexible after the lamination process.
Civil Engineering Tests Completed
As part of our third contract with the US Department of Transportation, our panels have been undergoing testing at the civil engineering department at Marquette University in Milwaukee, Wisconsin. They performed the following tests:
Shear testing
Freeze/Thaw cycling
Moisture conditioning
Accelerated load testing (simulates 15-years of truck abuse in 3-months)
They were so impressed by the results of the testing that they want to co-author a journal paper with us about the overall test program. We’ll be releasing the findings in a scientific engineering journal.
Summary
The Sandpoint pilot project gave us very valuable information: It allowed us time to tweak the LED intensity tables (the LEDs get brighter when the sun does likewise), adjust the heating profile with real time weather patterns, and taught us how to change our manufacturing process to solve the problems that were presented. It also pointed out the weaknesses in the SR3 panels, allowing us to finalize the SR4 design.
We decided from the very beginning of our Solar Roadways journey to be as transparent as possible. We realize that is not the way startups usually operate, but we wanted to be different. We are doing this work for the world and we wanted to allow our fan base to come along with us on the journey. Most people have realized that problems are part and parcel of the learning curve with inventing. We’ve been grateful to have so much support as we’ve worked to improve the panels and get them ready for mass production.
Since we’re done with the pilot project, and since the damaged cables are creating problems for the SR3 panels, we will shut down the Jeff Jones Square installation until spring, when we will replace the system with the new SR4 panels.
The first of the SR4 circuit boards have been received and tested. The first SR4 panels should be completed by the end of January. They will be tested extensively. We’ll put a few in our parking lot on Pine Street in Sandpoint, where everyone will be welcome to visit. Others will go to temporary exhibits. We just announced that one of those events will be the Treefort Music Festival in Boise in March. When the weather warms up in the spring we’ll replace the SR3 panels with SR4 panels at Jeff Jones Town Square in Sandpoint.
The SR4 will become the first commercially available Solar Road Panel.